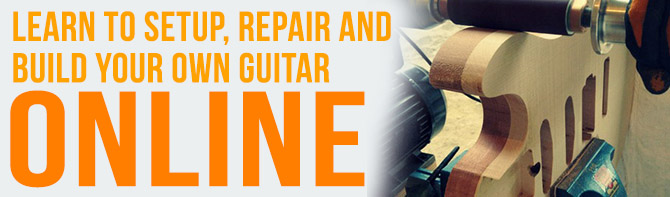
Visit the new website: www.buildyourownguitaronline.com
HOME > Neck through body guitar construction
NECK THROUGH BODY GUITAR CONSTRUCTION
If you're thinking of building a neck through insturment you've already made a great choice of sound: what you're looking for is great note definition and maximum sustain.
These are the characteristics that distinguish this type of construction from the raw and more "vintage" (but no less attractive) sound of the bolt on.
In the so-called "neck through" construction, the neck of the instrument is made up of a "sandwich" of wood that extends beyond the fretboard to form the central part of the body. Two "wings" are glued to the side of the neck to make up the body.
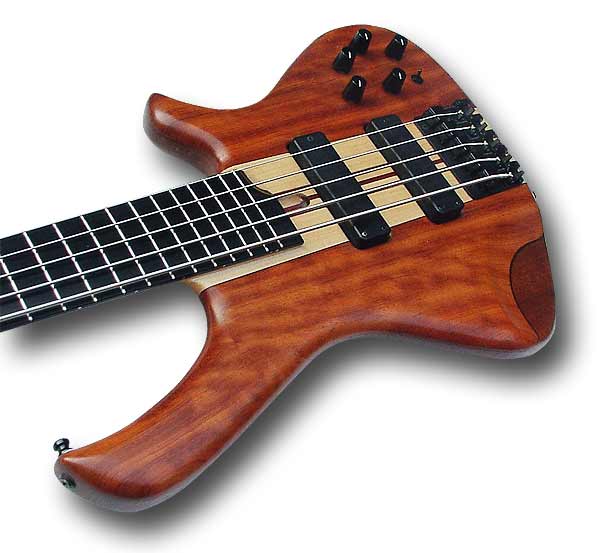
These are the characteristics that distinguish this type of construction from the raw and more "vintage" (but no less attractive) sound of the bolt on.
In the so-called "neck through" construction, the neck of the instrument is made up of a "sandwich" of wood that extends beyond the fretboard to form the central part of the body. Two "wings" are glued to the side of the neck to make up the body.
Neck through body construction means that the
neck is built with laminations of different woods
and extends throughout the entire length of the body to become the central part of it.
The vibration of the strings runs without interruption from the nut to the bridge, along a mix of different woods that makes up the neck, which is often also reinforced with carbon fibre bars because, not being replaceable in the event of breakage, it must be as strong as possible.
As well as providing rigidity, the layering of the neck with different woods, is intended to add the different peaks of resonance of each essence, resulting in a more defined and compressed sound.
This allows the guitar maker to calibrate the sound of the instrument to the taste of the musician by intervening ad hoc on the choice of woods that make up the "neck through" and the "wings" of the body.
Another advantage of the neck through construction is that the neck will be stiffer, shifting the resonance peak of the instrument BEYOND that of the notes on the fretboard and thus greatly reducing dead notes and "wolf notes".
All this, combined with the fact that the vibration of the string travels UNINTERRUPTED from the nut to the bridge, increases the stiffness of the neck by smoothing the note and increasing the sustain.
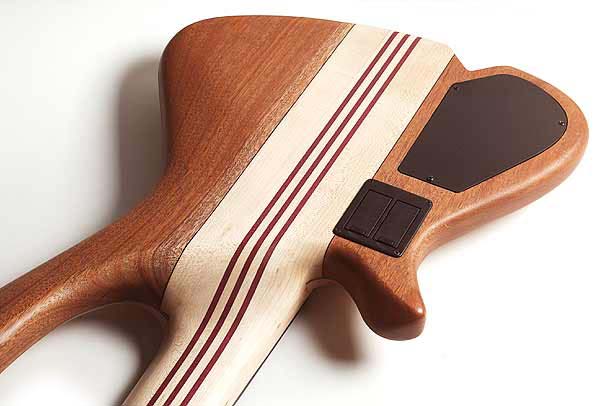
hard rock maple and purple heart.
NECK
Two types of wood are usually used when building of neck through necks: Canadian hard rock maple and Wenge.
I have spoken at great length about Canadian maple. This is without a shadow of a doubt the best wood ever for neck construction.
Wenge is slightly heavier than Canadian maple. Its characteristic density and rigidity make it very similar to maple in terms of cleanliness and sustain.
Wenge bends slightly more than the maple (so it absorbs more string vibrations) but it makes up for it with a greater density, so we can say that, at the level of sustain and vibration of the string, the two woods are equal. Being very dark in appearance, wenge is an excellent aesthetic alternative to maple.
These two main woods are matched with layers of other exotic woods such as mahogany, paduak or purple heart. All these woods together STIFFEN the neck, favouring sound transmission and creating wonderful chromatic alternations that embellish the instrument.
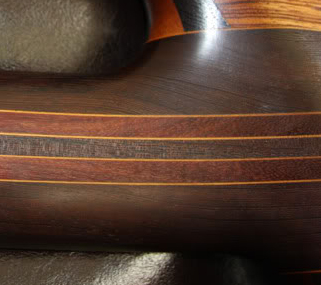
and purple heart creates an even more refined effect.
NECK LAMINATIONS
Each wood has its own peak resonance. Adding up the sounds of the various woods results in moving the resonance peak of the entire instrument upwards, moving it away from that of the strings frequency resonance.
This allows the neck not to interfere with the resonance of the strings to the benefit of the sound and a purer vibration.
The greater the number of laminations, the greater the sustain, and the more uniform the vibration of the string since the rigidity, an important factor, is greater. Generally, there is also a tendency to maintain an aesthetic compromise between rigidity and appearance. Too many laminations may appear "kitsch" and too few may not stiffen the neck enough.
For example, on the Frudua bass (see 2 photos above) I used a maximum of 7 laminations for the 5 strings and 9 for the 6 strings.
When gluing the various pieces that make up the neck, it is best to ensure that the vein, especially that of the two largest outer pieces, is glued so that the grain is mirrored (opposite). This solution will further increase the stability of the neck (see photo below).
In the necks made of wenge and purple heart, it is even possible to alternate the two woods with thin light maple veneers for an even more refined effect.
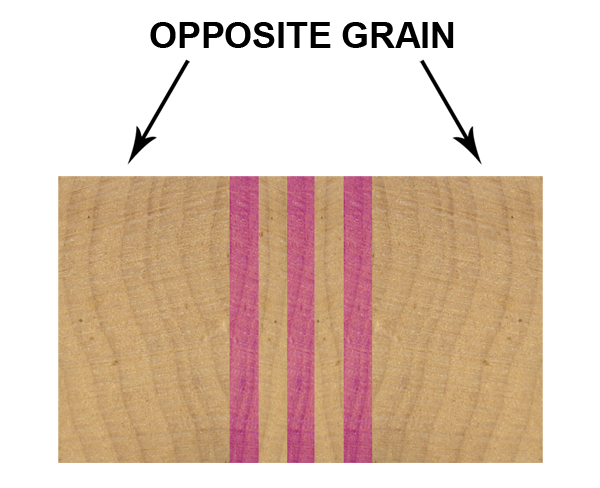
neck are glued with opposite grain to maximize stability.
BODY LAMINATIONS
In the "neck through" bass, the set of woods that make up the "wings" will affect the definition of the note, making it even more precise or adding body, depending on the woods used, and leaving unaltered the rest of the sound based on the neck’s structure.
Softer woods will give you more body while denser wood will give you more definition (especially on the 5th string).
The wings can be composed of a single piece or, in turn, a sandwich of two three or more different woods. The central part of the wings is called the "core" and is normally the thickest part. The thicknesses that are added above or below the "core" are called top plates or back plates, where the top plates are normally composed of exotic woods or even highly figurative flamed woods.
Based on what we have seen so far, we will have cut to the same measure all the pieces that will make up both the core and the top plate of the wings of the body.
First, let's define what kind of sound we're looking for. In the construction of the "neck through" bass we have mainly two great choices to make:
- opt for a very defined tonic sound, for which we will use a mahogany core and very hard wood such as bubinga, Zebrawood, purple heart, ebony and other exotic woods for the plates (this is an almost inevitable choice to strengthen the fifth string).
- or we can choose to use softer woods such as Alder and swamp ash (but my advice is never to go below the density of basswood) if the goal is to increase the body and punch of the sound (as for example in a fretless bass) or if we want to get a sound more suitable for the rock genre.
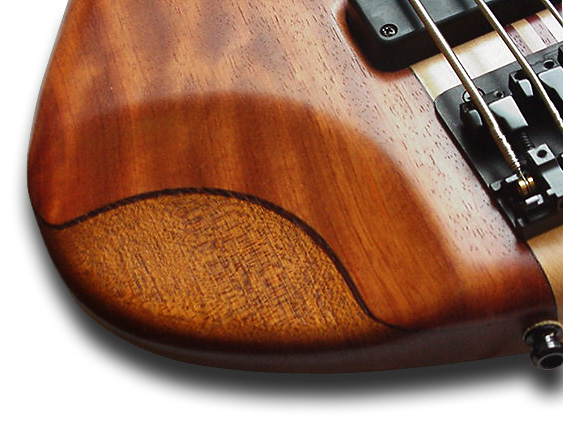
the "core" and between the neck and the body,
dark wenge or ebony acting aesthetically as a contrast
(pictured Frudua Slave Pentabass).
Let's start from the "core" (mahogany or alder) that represents the central wood (and more often in cm) of the wings that make up the body, and choose a wood that fits the sound we are looking for, for example:
These woods (except for American basswood) will still guarantee the bass the sufficient "body" for a balanced basic sound and would already be enough alone to obtain a high quality instrument with superior vibration purity even without the addition of tops or back plates.
We do NOT thin the neck too much. It would be better not to go below 23mm at the nut and below 26mm at the 12th fret. Let's reinforce the headstock with a volute under the nut and make sure that the neck/body joint is in turn well structured with an abundant amount of wood.
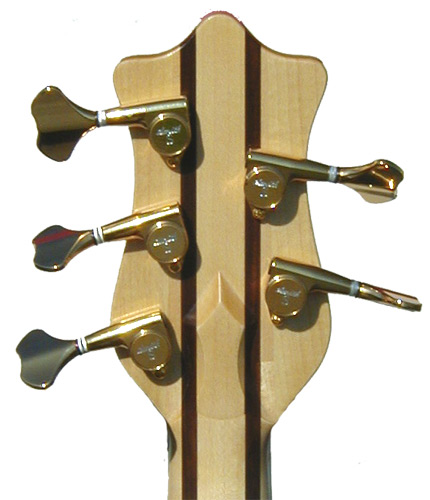
the neck and provides better tone and sustain.
TOP PLATES
Let's focus now on wood for the "top plates".
To understand how to choose wood according to the sound we want to obtain, imagine that we can equalize the sound molecularly, giving it more or less "body" (even on high notes), more or less sustain and more or less high depending on the rigidness of the wood that we are going to choose.
In general, the woods we are going to use (from maple up to particularly dense and hard exotic woods) give a rather sharp sound and increase the definition.
If we want to give the instrument punch and body, we choose a top plate that gives a lower sound to the tapping.
We opt for a top plate that at the tapping sounds acute if we want to give definition to the tonic for which to obtain a more defined attack on the note and strengthen the fifth string.
Between the core and the plates we can use a thin dark veneer of wenge or ebony that serves aesthetically as a thread.
TAPPING EXAMPLES
Here are some examples of how different top plates sound at tapping:
For more details on the choice and combination of woods, read these articles: "the sound of wood",
"matching woods"
and "the tapping technique".
SOME SUCCESSFUL MIX
Here are some combinations of woods that have proved very effective in 20 years of experimentation for the optimal compromise between the purity of vibration sustain, and body and definition of the note:
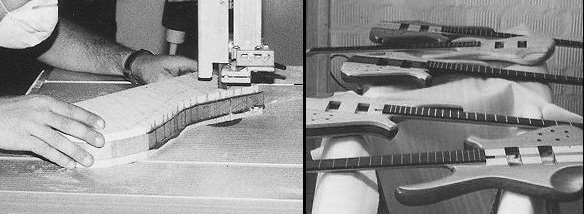
Note the wenge contrast veneer. Right various neck through
basses in the finishing process.